Inspections & Audits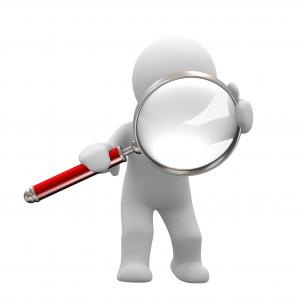
CALIFORNIA DEPARTMENT OF PUBLIC HEALTH (CDPH) - Annually:
The last 3 inspections by the CDPH have been excellent. Minor “fix on site” or sited violations include:
- Improper biohazard labeling of primary containers
- Red biohazard bag protrudes out of primary container obstructing biohazard labels
- Placement of articles/objects on top of primary/secondary containers
- Improper use of a red biohazard bag
CERTIFIED UNIFIED PROGRAM AGENCY (CUPA) - Every 1-3 years:
The last two CUPA inspections were good however the following violations were again found:
- Proper primary and secondary chemical container labeling. If the container is not empty, label its contents/hazards.
- Training Records, training records, training records. (Signatures both trainer and trainee). On chemical spill control, hazardous waste labeling/storage, emergency procedures (EAP)
- Hazardous chemical waste label does not have a start date and/or chemical(s) name(s) not spelled out.
- Hazardous chemical waste past 9 month (90 day-Acutely hazardous) disposal deadline.
CENTER FOR DISEASE CONTROL/FOOD AND DRUG ADMIN/US DEPARTMENT OF AGRICULTURE (CDC/FDA/USDA) - Periodic/Variable:
These regulatory inspections are usually site specific. Common concerns that need to be addressed during/after inspections include:
- Security and access to laboratory
- Authorized personnel list and contact information
- Good Laboratory Practices (GLP) protocol(s) design
CRANE AND HOIST INSPECTION - Quarterly and Annually
These inspections help insure that equipment is operating in safe manner with no broken or damaged components, protecting employees from the hazards associated with operating cranes, hoists and associated rigging. A list of Cal OSHA certifying agencies can be found within the Crane and Hoist Safety Program Manual.
- Initial Inspection and Certification -New, reinstalled, altered, repaired, modified, or overloaded cranes and hoists shall be inspected and load tested by a Certifying Agency prior to initial use. A certificate will be issued by the certifying Agency and must be retained by the department.
- Frequent Inspection - before use of equipment on a daily basis
- Periodic Inspection - quarterly and annual inspection meet this criteria
UCD BIOLOGICAL USE AUTHORIZATION AUDITS - Annually:
These campus Biosafety Office inspections are also site specific; however, there is standard audit that is used for most laboratories that have BUAs’. Some common issues:
- Training – BUA auditors are looking for BUA training which entails annual training on all the things associated with the BUA. (BUA document, Lab specific plans (BBP-ECP, MWMP, ATD), eyewash and shower location, Spill kit location and procedures.
- Annual review of plans: The person responsible for keeping up the plans needs to review them annually to make sure the information is still current.
- Biological spill kit has all the components it should - training is documented
UCD FIRE and LIFE SAFETY - Annually, all buildings:
Fire Inspections for laboratories/offices in the SVM over the past year have been very good. There were some issues that were corrected however here is a short list of violations that have been common to all facilities.
California Fire Code (CFC) |
Description |
5704.3.2.1.1 |
Storage of flammable liquids/materials in regular style refrigerators.
|
605.5 |
Use of extension Cords/flexible cords/surge protectors.
|
605.1 |
Frayed/broken power cords.
|
3.11 (2C) |
Storage/placement of file cabinets, boxes, desks, trash cans etc. in or near an exit, corridor or egress.
|
5003.7.3 |
Open flame/space heater used creating a hazardous condition.
|
INSTITUTIONAL ANIMAL CARE and USE COMMITTEE (IACUC) / ASSOCIATION FOR ASSESSMENT AND ACCREDITATION OF LABORATORY ANIMAL CARE (AAALAC) - Semi-Annual/Periodic/Triennial:
These campus (IACUC) and national (AALAC) inspections are done both in the laboratory/study area and the all animal facilities on the UCD campus to ensure proper animal care and use, animal housing by PI’s, staff, facility maintenance/ support, according to Public Health Services, USDA and UC Davis policies. Some campus and SVM deficiencies from past inspections/audits include:
- Security
- Training (Current and comprehensive for protocols)
- Protocol Availability (PPM 290-30)
- Expired pharmaceuticals/drugs
- Appropriate study records available
- Facility Issues (HVAC, room air exchanges, floors, periodic cleaning records, cage conditions etc.)
EHS LAB REVIEWS (INSPECT) - Annually:
These UCD campus inspections are the laboratory reviews done annually by EH&S as required by UCD and UCOP audited by the EH&S Safety Professional assigned to the SVM. Principle Investigators must submit resolutions to violations found by use of the Safety Inspection Tool (SIT) online. The school has been very good in these inspections with the following items commonly found:
- Secondary chemical containers not clearly labeled with chemical name and primary hazard(s).
- Laboratory personnel have not completed UC Laboratory Safety Fundamentals training.
- Fume hood audible/visual alarm is non-functional or visual airflow indicator is not working.
- Fume hood has not been certified within the past year.
SELF-INSPECTIONS (either SVM INTERNAL (VMDO) LAB AUDIT OR USING INSPECT SELF-INSPECTION TOOL - Annually:
The annual self-inspections performed by the SVM Safety Program and INSPECT tool are for internal purposes only and satisfy the Cal Code of Regulations (8 CCR, Sec 3203) and the UCD Policies and Procedures Manual (PPM) Sec 290-15 and is part of the departmental IIPPs as required. Examples of some corrections needed from past audits:
- Updated laboratory operational documentations (IIPP, EAP, MWMP, CHP, Chemicals, LHAT, SOPs, etc.)
- Training records/ Lab-specific training (all lab personnel) need to be current/up to date
- Incompatible chemical storage (both dry and liquid)-secondary containment
- Secondary chemical containers not clearly labeled with chemical name and primary hazard(s).